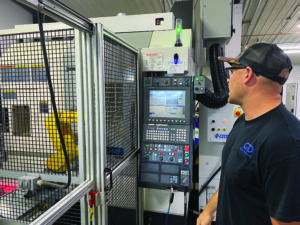
by Eric Dietrich
Deputy Editor / Reporter, Montana Free Press
Tucked off U.S. Highway 93 in the Bitterroot Valley, in a nondescript building with mountains rising behind it, is a 21st-century boutique factory.
The lobby of the second-generation family business, Glacier Tool, was filled with friendly dogs on a weekday morning in June. Behind it, on the brightly lit production floor, workers wearing safety glasses huddled around car-sized machines, intent on clipboards and measuring instruments. The room was filled with the whirr of high-speed metal cutting bits and the hiss of pneumatic air.
Part of what keeps the business growing in this stretch of rural Montana, blessed with scenery but missing many of the advantages that would come with operating near a big-city manufacturing hub? Robotics.
Glacier Tool, owner Cody Dolce said, specializes in small, precisely machined metal components, producing them hundreds or thousands at a time. Most of its business is firearms parts — firing pins, scope supports and other intricate pieces that will eventually be assembled elsewhere into rifles and grenade launchers, supplying both the U.S. military and civilian firearm companies. At times, Dolce said, the shop has also produced mining equipment and medical device components.
In contrast to places like the industrialized Midwest, the Bitterroot Valley doesn’t have a large labor pool of skilled machinists for manufacturing companies to draw on, nor the workforce necessary to staff the labor-intensive production lines of America’s big industrial centers. And those workforce challenges constrained the company, Dolce said, even before the COVID-19 pandemic put the screws to Montana’s labor market, pushing unemployment to historic lows and turning recruiting into a top-of-mind worry for businesses across the state.
Back the 1980s, when Dolce’s parents, Gary and Peggy, started the business out of their garage in Lolo, the company was hi-tech for its time, forging into the then-fledgling world of using computers instead of machinists’ hands to guide the cutters that shape metal into useful components. As he’s taken over the business, Dolce has doubled down on investing in automation, using robotics and computer-controlled production machines to keep growing without adding more workers.
The key moment, he said, came back in 2012 when Glacier Tool won a U.S. Department of Defense contract to produce trigger hammers for M16 rifles. The initial order was for 65,000 parts, but it came with the potential to expand the contract to as many as 480,000 — well beyond what Glacier could produce without scaling up its operation.
“It was at that point we realized we had to do something a little different,” Dolce said.
The company responded by moving to a bigger building and investing in a fully automated production “cell,” a computer-controlled milling machine equipped with a robotic arm that can swap rough-cast metal parts on and off the fixture that holds them in place while they’re trimmed to their final dimensions.
Once the setup is dialed in for a specific part, the cell can single-mindedly churn through a production run unattended, pulling from unmachined castings arrayed on a small conveyor belt.
Dolce said the company’s human staff commonly tees up that and other automated production cells during the workday, leaving them to run overnight. That lets Glacier maximize its production without employees working long hours.
When the company first installed the machine, Dolce said, one of his employees asked if their job was going to be automated out of existence. Dolce said he doesn’t see it like that — instead, automation shifts workers away from rote tasks like loading and unloading machines, freeing them for more sophisticated work like quality control checks and troubleshooting.
“It empowers people not to just be an operator,” Dolce said.
Automation, he said, also helps him pay his employees better so their careers remain viable despite Montana’s rising cost of living. The company’s headcount has stayed fairly constant at about 15 workers since it started pushing into automation, he said. While he used to be able to pay experienced workers about $25 an hour, he’s now able to pay into the “mid-30s.”
“We’re essentially gaining a second and even a third shift,” Dolce said, “so we’re able to pay more for a guy who’s working on a single shift.”
Montana business leaders and lawmakers have in recent years increasingly touted automation as a key strategy for Montana’s manufacturing sector, particularly as businesses try to adjust to the realities of the state’s post-COVID workforce.
Last year, the administration of Gov. Greg Gianforte put $6 million of the state’s COVID stimulus dollars toward a loan program intended to help manufacturing businesses invest in automation, redirecting dollars that had previously been earmarked for a workforce-training grant program that was drawing little interest. While labor unions objected to the shift, administration officials argued the money would help employers retire back-breaking manual labor jobs that are increasingly hard to fill.
Gianforte spokesperson Kaitlin Price said that as of late June the administration was still working to finalize the automation loans. She noted the program has involved coordinating with both recipient businesses and third-party lenders.
Glacier Tool still has a few comparatively old-school machines on its premises — some kept mostly to make spare parts for maintenance jobs — but it’s been investing in more automated production in recent years.
Dolce said that even though automated milling machines come with six-figure price tags, they’re able to generate enough revenue to recoup their purchase price with six or seven months of work.
Glacier Tool had considered participating in the state loan program as it prepared to purchase its latest automation cell, Dolce said, but eventually decided to pull the trigger without that assistance. He now expects the business to ship between 15,000 and 20,000 parts a month this year.
None of the company’s suppliers or customers are located inside Montana, Dolce said, but the Bitterroot is where he was as born and raised — and he doesn’t see any good reason to relocate someplace else.
“With FedEx and UPS, geographically we can be anywhere,” he said.
Editor’s note: This story was produced through MTFP’s summer reporting residency program, which is temporarily placing staffers in small newsrooms across the state to help them better understand the ins and outs of different corners of Montana. Deputy Editor Eric Dietrich reported this article while spending a week in June 2023 based out of the Bitterroot Star newsroom in Stevensville.